2
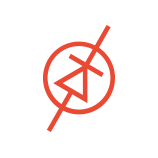
I built a choke coil out of a MOT which was recommended in another post to reduce ripple voltage in my electric kiln project and was surprised by how LOUD it was. I have placed it on a piece of plywood with a rubber material between the coil and the wood to help reduce vibration. It's better than...